In recent years, audits at ethanol plants by the United States Environmental Protection Agency (EPA) and state regulatory representatives have resulted in notice of violations (NOVs), fines, and an open door for additional permit violations. Regulatory site visits have often focused on the components located on top of the beerwell and fermenters (agitators, pressure relief devices, and connectors). Using optical gas imaging (OGI) equipment, auditors look for leaking components that can be associated with uncontrolled vapor emissions. Uncontrolled vapor emissions from beerwell and fermentation tank top equipment can have significant economic impacts, including product loss, compliance fines, increased permit requirements, enhanced emissions monitoring programs, or process improvement requirements.
Trihydro assists facilities nationwide with their voluntary and permit-required beerwell and fermentation top monitoring programs and has gathered insights on potential emissions. In this article, we review potential regulatory impacts from beerwell and fermentation tank top emissions, present the most common leaking components, and highlight best practices for managing emissions from beerwell and fermentation tank top equipment.
Regulatory impacts from beerwell and fermentation tank top emissions
EPA’s Clean Air Act (CAA) penalty policy for emissions violations has two main components:
- Economic benefit
- Gravity of the violation
Penalties under the economic benefit component can be relatively low and EPA’s litigation teams have discretion in choosing not to pursue penalties under $5,000. Penalties related to the gravity of the violation component involve more complex calculations and can have a greater monetary impact. The gravity calculation includes six factors:
- Regulatory importance
- Toxicity of pollutants
- Size of violator
- Level of violation
- Duration of violation
- Sensitivity of environment for State Implementation Plan (SIP) and New Source Performance Standards (NSPS) cases
Regulatory importance is subjective and can add up to $15,000 to a penalty, while and toxicity of pollutants can add $15,000 per hazardous air pollutant (HAP). The figures below show the factors for size of violator, level of violation, and duration of violation as taken from the Clean Air Act: Stationary Source Civil Penalty Policy: October 25, 1991 (policy):
Figure 1: Size of Violator
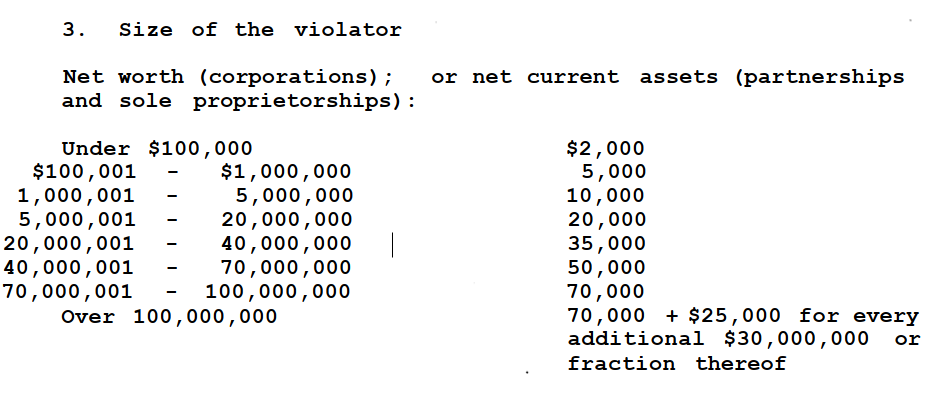
Figure 2: Level of Violation
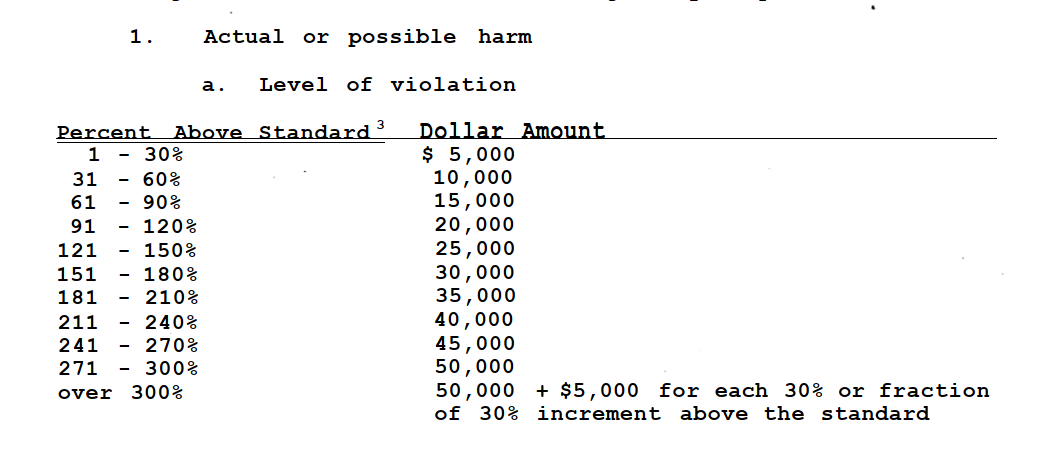
Figure 3: Duration of Violation
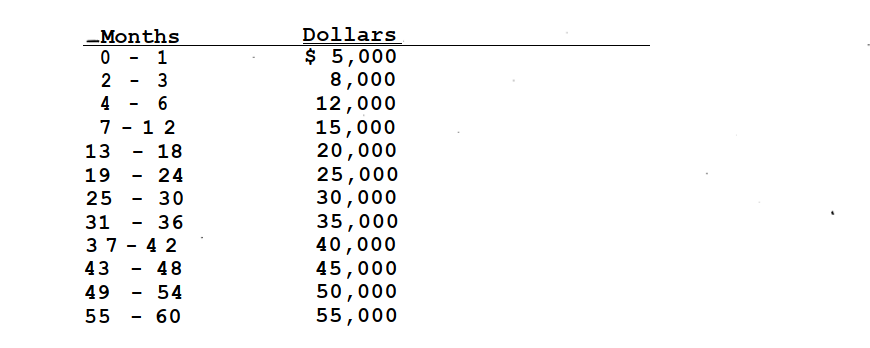
Additional violations are included in the policy that could be evaluated if issues are found.
Common beerwell and fermentation tank top component leaks
Agitator seals and pressure relief valves (PRVs) tend to be the most common leak locations. If these components are allowed to emit, it can result in violations for exceeding permitted emission limits, product loss, or other regulatory agency stipulated penalties.
Agitator leaks generally result from an issue with the seals/packing. PRV leaks tend to stem from a deteriorated seal, which allows vapors to escape.
Adding these components to routine inspections can help mitigate potential regulatory impacts and can help with tracking and scheduling routine maintenance.
Managing emissions from beerwell and fermentation top component leaks
Increased regulatory attention and the improved ability to visualize leaks through OGI have led several facilities to implement voluntary emissions monitoring programs. Voluntary monitoring programs not only assist with compliance efforts, but can help identify components requiring maintenance.
The risk potential for emissions from components located on the tops of the fermentation tanks and beerwell arises from the lack of routine leak detection and repair (LDAR) requirements. Components on top of fermentation tanks and beerwells are typically primarily in CO2 service, with relatively low concentrations of volatile organic compounds (VOCs) and HAPs. As such, the components are generally not subject to LDAR regulations and have not historically been subject to routine inspection.
Because OGI equipment allows auditors to survey more equipment in less time, auditors have expanded the areas inspected for emissions during their time on-site. If emissions are found during an audit, a lack of data to support when a leak likely began can result in the regulatory agency using a longer length of time to calculate violation penalties, or could lead to arguments that the scrubber system is not achieving proper capture of CO2, leading to possible major source provisions. By implementing voluntary routine monitoring for components located on top of the beerwell and fermentation tops, facilities can track when equipment begins to leak and address it before the leak becomes an emissions issue.
Voluntary inspections can be done via OGI or Method 21 (M21), and the components can be placed on a schedule that aligns with existing routine inspections. While OGI provides visual representation of emissions, M21 can be more cost-effective.
Conducting routine inspections of the beerwell and fermentation top components provides owners and operators with up-to-date data and records of emissions, and can help minimize the duration of potential emissions to be calculated in the event of an audit. Voluntary emissions programs can also help owners and operators prioritize equipment maintenance, preventing emissions.
Interested in more information?
Our experience assisting clients with the increased regulatory interest at ethanol plants has allowed us to gather fermentation top monitoring data and insights that can be used to develop and refine monitoring programs. Contact us today to discuss your site-specific needs.
Come see us at the 2021 Fuel and Ethanol Workshop
Trihydro will be attending the Fuel and Ethanol Workshop and Expo July 13-15, 2021 in Des Moines, Iowa. Stop by booth #1332 to discuss beerwell and fermentation top component considerations with our team members.